Unsteady Analytical Model for Appendix Gap Losses in Stirling Cycle Machines
Appendix gap losses may amount to approximately 10 % of the heat input to a Stirling engine. They are caused by the annular gap between the insulating dome of a piston or displacer and the adjacent cylinder wall. The aim of this work is to develop a new analytical model for these losses, since the existing modeling approaches appear to be insufficient and are partly based on very gross and possibly questionable assumptions.
Description
For the design of a Stirling cycle machine a high-accuracy model is needed. Recent experimental results [1] indicate that the thermal losses associated with the cylinder system, particularly those caused by the annular gap around the displacer, have been underestimated in their influence on the engine performance. Therefore, existing models for these thermal losses, which are commonly referred to as appendix gap losses, have been reviewed [2]. The analytical approaches are of major importance, as they may allow the derivation of practically applicable design formulas for the gap geometry. The previously available models appear to be partly based on questionable assumptions. Therefore, a new analytical model will be developed. It has been shown that the flow in the gap is laminar but unsteady [2], and that analytical solutions for the flow pattern and the temperature profile can be directly derived from the conservation laws. Herewith, the new model will be able to consider inertia effects in the unsteady flow of the gas in the gap. In contrast to an existing solution [3], which is based on the assumption of a pure drag flow (Couette flow), the new model will also take into account the evidently prevailing pressure-driven flow (Poiseuille flow) component. Additionally, all energy transport mechanisms in the cylinder system will be investigated with respect to their dependency on the axial position. Hereby, the simplifying assumptions of constant wall and gas temperature gradients along the gap, which is made in all previous models, will be checked, since earlier temperature measurements at Stirling machine cylinders and numerical simulations suggest the expectation of a curved cylinder wall temperature profile instead.
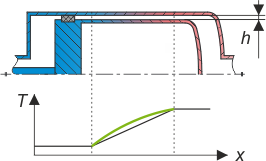
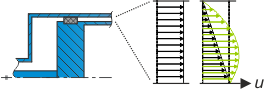
References
[1] | Heikrodt, K. und R. Heckt: “Gasbetriebene Wärmepumpe zur monovalenten Raumbeheizung und Trinkwassererwärmung” BVE Thermolift GbR: 241, Aachen, 1999 http://edok01.tib.uni-hannover.de/edoks/e001/303037180.pdf |
[2] | Kühl, H.-D.: “Wärmetransformationsprozesse ohne Phasenumwandlung - thermodynamische Konzeption, Auslegung und Optimierung an Beispielen aus der Wärmepumpen- und Kältetechnik” Habilitation theses, University of Dortmund, 2003 http://hdl.handle.net/2003/2798 |
[3] | Kühl, H.-D., I. Geue: “Application of Similarity-Based Scaling to the Design of an Experimental, Laboratory-Scale Convertible Stirling-Vuilleumier Hybrid Engine” Proc. 7th IECEC, Denver, CO, AIAA, 2009 http://pdf.aiaa.org/preview/CDReadyMIECEC09_1894/PV2009_4539.pdf |
[4] | Geue, I., J. Pfeiffer, J. Hötzel und H.-D. Kühl: “Design of an Experimental Convertible Stirling-Vuilleumier Hybrid System Obtained by Similarity-Based Scaling” Proc. 14th ISEC, Groningen, 2009 |
[5] | Geue, I., J. Pfeiffer und H.-D. Kühl: “Experimental Results of a Novel Laboratory-Scale Stirling-Vuilleumier Hybrid System” Proc. 9th IECEC, San Diego, AIAA, 2011 |